CNC Lathing Parts Suppliers: Your Guide to Quality and Precision
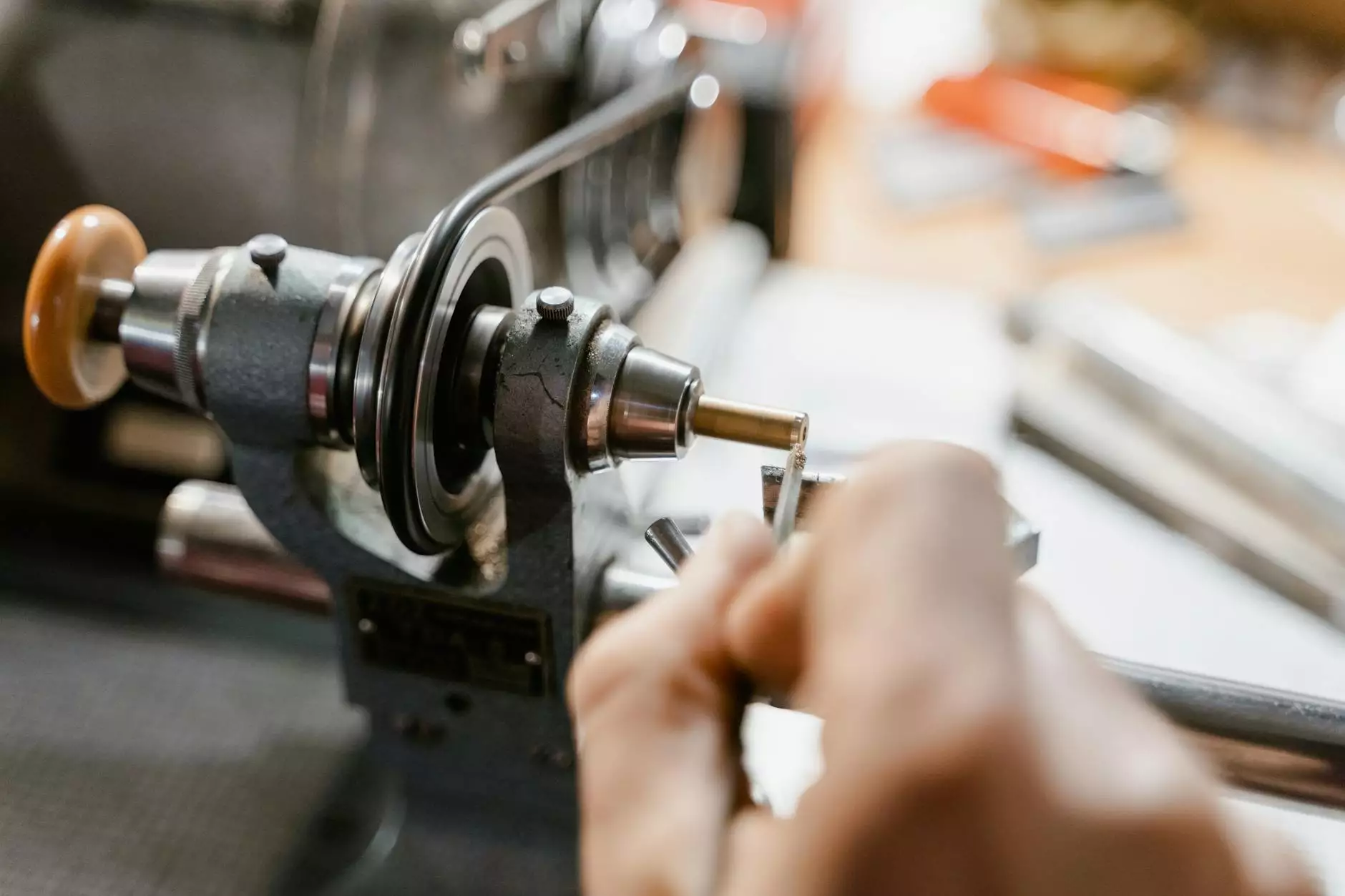
CNC lathing parts suppliers play a pivotal role in the manufacturing industry, especially in sectors that require high precision and efficiency. Understanding the vital aspects of CNC (Computer Numerical Control) lathing and how to choose the right suppliers can lead your business towards success and innovation. This article serves as an in-depth guide to navigating the world of CNC lathing parts and finding the best suppliers for your manufacturing needs.
What is CNC Lathing?
CNC lathing is a computer-controlled manufacturing process where a rotating workpiece is shaped by a fixed cutting tool. This technology offers unparalleled precision and versatility, allowing manufacturers to create intricate designs efficiently. The use of CNC machines enables parts to be produced at a higher rate with less human error, resulting in a streamlined workflow.
The Advantages of CNC Lathing
- High Precision: CNC machines can produce components with tolerances as tight as +/- 0.001 inches.
- Consistency: Each part produced is identical, maintaining quality across mass production.
- Complex Shapes: CNC lathing allows for the manufacturing of complex geometries that may be difficult with traditional lathing methods.
- Reduced Waste: The precision of CNC machining minimizes material waste, making it more economical.
- Automated Production: CNC lathing reduces the need for manual intervention, allowing for 24/7 operation and increasing productivity.
Identifying Reliable CNC Lathing Parts Suppliers
Choosing the right cnc lathing parts suppliers can significantly impact the quality of your final product. Here are key factors to consider when shortlisting potential suppliers:
1. Quality Certifications
Ensure that the suppliers hold relevant quality certifications, such as ISO 9001, which demonstrates adherence to international quality standards. These certifications indicate a commitment to quality control and consistent manufacturing processes.
2. Experience and Reputation
Research the supplier’s experience in the industry. A supplier with a solid track record and a reputation for delivering high-quality products is likely to contribute positively to your manufacturing process. Look for client testimonials and case studies to gauge their reliability and performance.
3. Range of Services Offered
Some suppliers may specialize in specific types of lathing or materials. Make sure the supplier you choose can handle the specific requirements of your projects, whether that involves various metals, custom designs, or rapid prototyping.
4. Technological Capabilities
Evaluate the technology and equipment that the supplier uses. Advanced CNC machines that incorporate the latest software and hardware can enhance production efficiency, precision, and ultimately, the quality of the parts produced.
5. Customer Service and Support
Effective communication and support from suppliers can significantly ease the manufacturing process. Ensure that your selected suppliers provide comprehensive customer service, including assistance with design, technical issues, and delivery logistics.
The Role of Metal Fabricators in CNC Lathing
Metal fabricators are integral to the CNC lathing process. They work alongside CNC lathing parts suppliers to ensure that the parts meet specific industry standards and client requirements. The fabricators create the designs and specifications that CNC machines follow, which manifests in the final products used in various applications, from automotive to aerospace.
Collaboration Between Suppliers and Fabricators
The synergy between cnc lathing parts suppliers and metal fabricators leads to successful project outcomes. This relationship fosters innovation, allowing for rapid design changes and iterative improvements to meet client demands promptly.
Common Applications of CNC Lathing Parts
CNC lathing is utilized in a wide range of industries. Here are some of the most common applications:
- Aerospace: Precision components for aircraft, such as brackets and landing gear parts.
- Automotive: Custom parts and assemblies for vehicles, including engine components and fittings.
- Medical: Surgical instruments and implants made with high precision and quality standards.
- Electronics: Housings and components for electronic devices that require intricate designs and specifications.
- Industrial Machinery: Parts for heavy machinery used in manufacturing and construction.
Future Trends in CNC Lathing and Metal Fabrication
The future of CNC lathing and metal fabrication is promising, driven by technological advancements and evolving industry demands. Some of the critical trends to watch include:
1. Automation and Robotics
The integration of robotics in CNC lathing processes is expected to enhance efficiency and reduce labor costs. Automated systems can manage repetitive tasks, allowing human operators to focus on more complex aspects of production.
2. Increased Use of IoT
The Internet of Things (IoT) is becoming increasingly prevalent in manufacturing. Connected machines can provide real-time data and analytics, improving maintenance schedules and reducing downtime.
3. Sustainability Initiatives
As environmental concerns grow, CNC lathing suppliers and metal fabricators are focusing on sustainability. This includes utilizing recyclable materials, implementing energy-efficient processes, and reducing waste.
4. Advances in Materials
Research into new materials such as lightweight composites and alloys is expanding the possibilities for CNC lathing. These materials can lead to stronger, lighter components with enhanced performance characteristics.
How to Approach Your Supplier Relationship
Building a strong relationship with your cnc lathing parts suppliers is essential for long-term success. Here are some strategies to consider:
1. Open and Transparent Communication
Maintain an open dialogue with your suppliers. Share your project goals, timelines, and potential challenges. A collaborative approach encourages suppliers to provide better solutions tailored to your needs.
2. Regular Performance Reviews
Conduct regular assessments of your supplier’s performance. Evaluate factors like quality, delivery timelines, and communication efficiency. This can help identify areas for improvement and strengthen the partnership.
3. Development of Joint Solutions
Engage in collaborative problem-solving when challenges arise. This not only fosters a sense of partnership but also enhances innovation and efficiency in your projects.
Conclusion
In conclusion, selecting the right cnc lathing parts suppliers is crucial for any business involved in manufacturing. By understanding the intricacies of CNC lathing, identifying reliable suppliers, and leveraging the advantages of collaboration, you can enhance your production capabilities and drive your business forward. Remember to stay informed about industry trends and advancements in technology to maintain a competitive edge in the market. By prioritizing quality and precision in your parts production, your company will be well on its way to achieving manufacturing excellence.