Prototype Model Maker en France
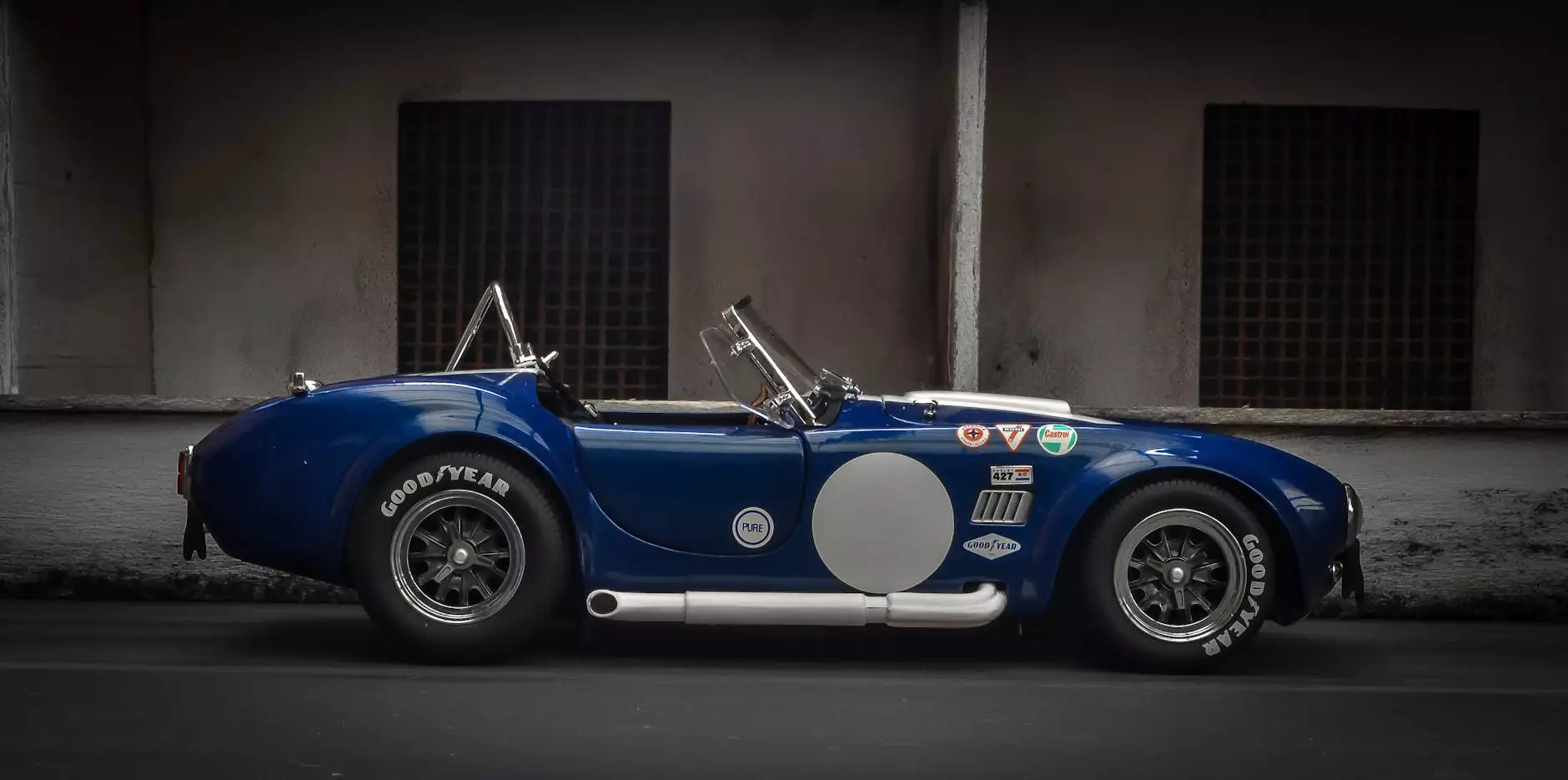
Prototype model makers en France play a crucial role in various industries, including architecture, design, and engineering. These skilled artisans and technicians are typically responsible for creating scale models that represent real-world objects, concepts, or places. This article delves deep into the intricacies of prototype model making, the tools and materials used, and the significance of this craft in France and beyond.
The Role of Prototype Model Makers
The role of a prototype model maker encompasses a wide range of responsibilities. They are not merely builders; they are creative problem solvers who bring ideas to life. The importance of their work can be broken down into several key functions:
- Visual Communication: Models serve as a visual representation of concepts that might be difficult to convey through words or drawings. This is especially important in architecture, where clients may struggle to envision a completed project.
- Design Validation: Prototyping allows designers to test their ideas and make adjustments before finalizing a concept. This iterative process can save time and money by identifying potential issues early on.
- Collaboration: Prototype model makers often work closely with architects, engineers, and designers. Their feedback can lead to innovative solutions, enhancing the overall quality of the final product.
- Client Presentations: Having a tangible model aids in client presentations, making it easier to explain complex designs and garnering approvals.
The Importance of Prototype Models in Architecture
In the field of architecture, the role of prototype model makers is indispensable. Models can vary from small scale representations to large, intricate designs. Here are some reasons why they are vital:
1. Enhancing Artistic Vision
Architectural models provide a physical object for architects to work with, allowing for a greater understanding of how the space will interact with its environment. An expertly crafted model can enhance an architect's artistic vision, showcasing the intended materials, light, and ambiance of a project.
2. Environmental and Urban Studies
Models are also used in urban studies to evaluate the impact of new buildings within existing communities. This encompasses aspects of environmental design and sustainability. A well-designed prototype can identify how structures will affect the surrounding area, including human interactions and ecological balance.
3. Regulatory Approvals
In France, presenting prototype models can facilitate the regulatory approval process. Local governments often require visual representations to assess the compatibility of new constructions with existing urban fabric.
Techniques and Materials Used in Prototype Model Making
French prototype model makers employ various techniques and materials to create their masterpieces, depending on the project’s needs. Here’s an overview of commonly used techniques and materials:
1. Traditional Handcrafting vs. Digital Technologies
While many traditional model making techniques remain popular, the rise of digital technologies has transformed the industry. 3D printing, for example, allows for precise and intricate structures that would be impossible, or at least extremely difficult, to create by hand. Model makers often use a blend of both methods to optimize their processes.
2. Common Materials
- Wood: Lightweight and easy to work with, wood is often the primary choice for prototyping, especially for architectural models.
- Plastic: Various plastics are used, as they can be cut and shaped easily, and are available in numerous colors.
- Foam: Commonly used for base models, foam is lightweight and readily available, allowing for quick adjustments.
- Metal: More durable models might incorporate metals, particularly in engineering prototypes where strength and resilience are critical.
The Creative Process of Prototype Model Making
Creating a prototype is an intricate process involving several stages, from conceptualization to final touches. Here’s an overview of the creative journey:
1. Conceptualization
The first step involves understanding the project scope and requirements. This means gathering information, sketching ideas, and, in many cases, discussing with clients or the design team to ensure alignment on the vision.
2. Design and Planning
Once the concept is clear, the planning phase begins. This often involves drafting detailed drawings and selecting materials, tools, and techniques for construction. Prototype model makers in France take particular care to ensure that their designs accurately reflect the intended final product.
3. Construction
The construction phase can take significant time and skill, as it involves cutting, shaping, and assembling the chosen materials. Attention to detail is imperative during this phase since minor errors can compound in the final model.
4. Finishing Touches
After the basic structure is complete, attention turns to the details. This might include painting, adding textures, or inserting lighting—elements that bring the model to life and ensure it’s an accurate representation of the intended project.
Challenges Faced by Prototype Model Makers
Every profession has its challenges, and prototype model making is no exception. Some common obstacles faced by practitioners in France include:
1. Balancing Quality and Cost
Often, there’s pressure to reduce costs while maintaining high quality. Achieving this balance requires creativity, resourcefulness, and sometimes compromising on materials without sacrificing the integrity of the prototype.
2. Keeping Up with Technology
As technology continues to evolve rapidly, model makers must stay updated with new tools and techniques to remain competitive. This might involve investing in training or new equipment, which can be a challenge, especially for small businesses.
3. Meeting Tight Deadlines
The creative process can be time-consuming, and balancing a tight schedule can lead to stress and compromised quality. Efficient time management and streamlined processes are vital.
Why Choose a Prototype Model Maker en France?
Choosing a qualified prototype model maker in France offers numerous advantages. Here are a few compelling reasons:
1. Expertise and Experience
Professionals in France bring a wealth of expertise and experience. Many have years of training in specialized schools and workshops, ensuring quality craftsmanship and innovative solutions.
2. Access to Local Materials
Working with a local prototype model maker means they have established relationships with suppliers, allowing for easier access to high-quality materials sourced within France.
3. Cultural Context
French prototype model makers understand the cultural context and aesthetic preferences unique to France. This local knowledge translates into models that resonate with not only French clients but also international audiences.
Conclusion: The Future of Prototype Model Making in France
The field of prototype model making en France is evolving, driven by technological advancements and an ever-growing demand for precision and quality in design. As industries continue to intertwine, from fashion to architecture, the necessity for skilled model makers will remain paramount.
Investing in a prototype model maker offers unparalleled insight and creative support that can enhance any project, making it fundamental for professionals looking to push the envelope of design and innovation. With a robust tradition of craftsmanship and a forward-looking mindset, France stands as a beacon for talented prototype model makers, ensuring that this art form will thrive for generations to come.