The Evolution and Impact of Automotive Plastic Injection Molding Companies
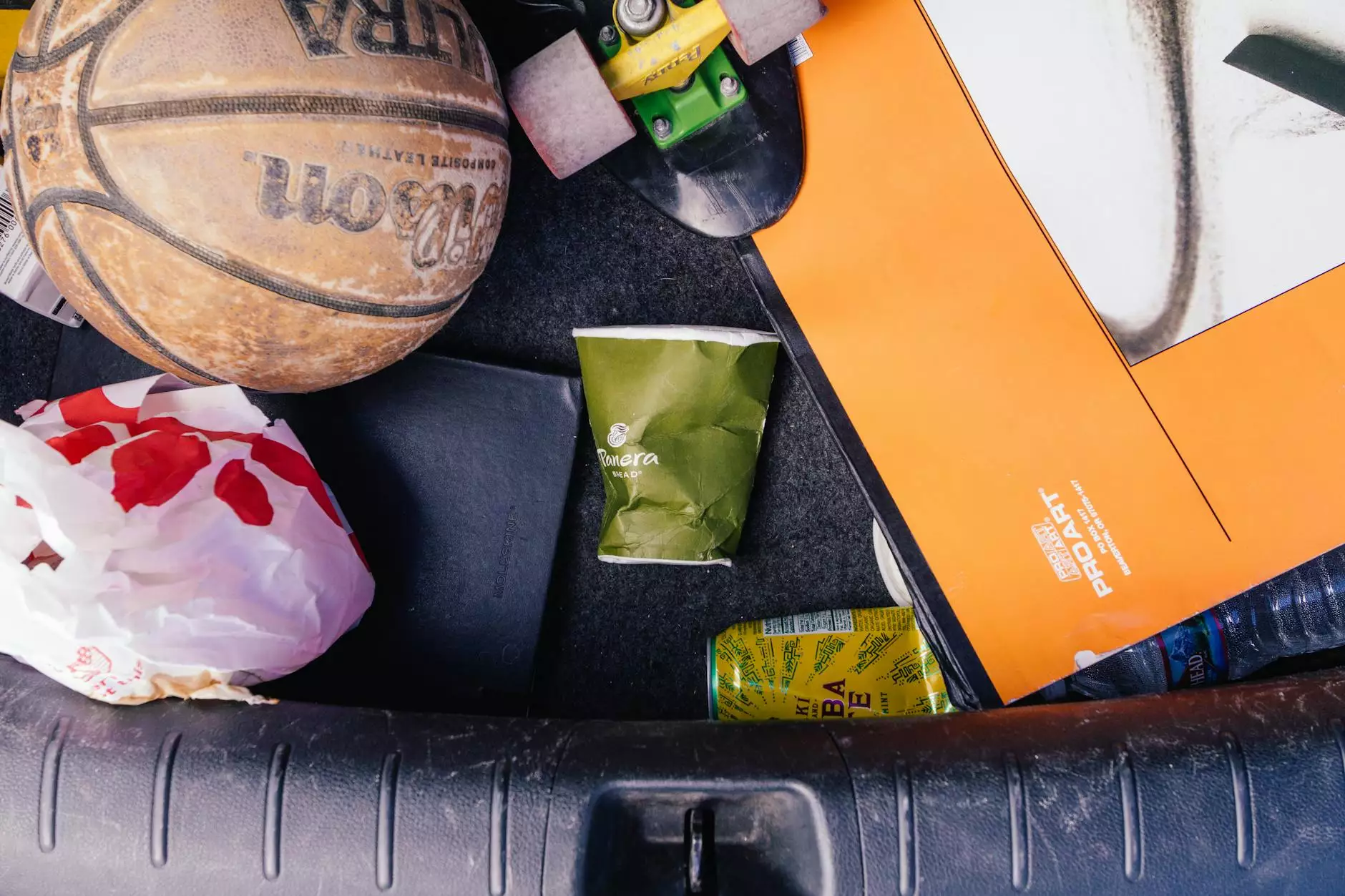
The automotive industry is in a constant state of transformation, with technology influencing everything from engine performance to vehicle aesthetics. One of the technological advancements that has significantly reshaped this industry is automotive plastic injection molding. As we delve into this topic, we will explore how automotive plastic injection molding companies are paving the way for innovation, efficiency, and sustainability in vehicle production.
Understanding Automotive Plastic Injection Molding
Plastic injection molding is a manufacturing process that involves injecting molten plastic into a mold to produce parts and components. This technique is favored in the automotive industry for several reasons:
- Precision Engineering: The process allows for intricate designs and rapid production cycles.
- Material Versatility: A wide range of plastics can be used, catering to various performance requirements.
- Cost Efficiency: Reduced waste and lower labor costs lead to significant savings for manufacturers.
Given these advantages, it's no surprise that automotive plastic injection molding companies are integral to modern vehicle manufacturing.
Benefits of Plastic Injection Molding in the Automotive Sector
The use of plastic injection molding is not merely a trend but a strategic choice that comes with a host of benefits:
1. Enhanced Design Flexibility
The ability to create complex shapes makes plastic injection molding a preferred option for automotive components. Manufacturers can produce aesthetically pleasing and functional parts that meet both consumer preferences and regulatory requirements.
2. Superior Product Consistency
Due to the automation involved in the injection molding process, companies can achieve a high degree of consistency in production. This level of quality control ensures that every part meets strict automotive standards, minimizing defects and enhancing overall vehicle reliability.
3. Lightweight Nature of Plastic Components
Automakers are increasingly seeking ways to reduce vehicle weight to improve fuel efficiency. Plastic parts produced via injection molding are significantly lighter than their metal counterparts, contributing to reduced emissions and enhanced performance.
4. Sustainability and Eco-Friendly Options
Many automotive plastic injection molding companies are now using recycled materials or bioplastics in their processes. This shift not only supports sustainability initiatives but also appeals to environmentally conscious consumers.
Key Players in the Automotive Plastic Injection Molding Industry
The automotive plastic injection molding landscape features several key players that are dominating the market. These companies are renowned for their commitment to quality, innovation, and customer satisfaction. Here are a few examples:
- Deep Mould: Known for quality and precision, Deep Mould leads the way in providing customized solutions for the automotive sector.
- Röchling Group: A global leader specializing in high-performance plastics, Röchling contributes to weight reduction and resource efficiency in vehicles.
- GESIPA: Focused on innovation in metal and plastic components, GESIPA excels in providing sustainable solutions for automotive manufacturers.
These companies set benchmarks for excellence, driving the industry forward.
Challenges Faced by Automotive Plastic Injection Molding Companies
While the benefits are plentiful, the journey is not without its challenges. Companies in the sector face several hurdles:
1. Material Sourcing and Costs
The volatility of material prices can pose a significant challenge for manufacturers. Plastic resins can fluctuate in availability and cost, affecting overall production budgets.
2. Technological Advancements
Staying abreast of the latest technology in molding techniques and materials can require substantial investment. Companies must continually innovate to remain competitive.
3. Environmental Regulations
As regulations around sustainability become more stringent, companies need to ensure compliance while maintaining cost-effectiveness. Transitioning to eco-friendly materials can be complex.
Best Practices for Automotive Plastic Injection Molding Companies
To navigate these challenges and thrive, automotive plastic injection molding companies can adopt several best practices:
- Embracing Innovation: Invest in the latest technologies, such as advanced molding machines and computer-aided design software.
- Enhancing Collaboration: Partner with suppliers and clients to optimize material sourcing and design processes.
- Focusing on Sustainability: Explore the use of recycled materials and sustainable practices in manufacturing.
The Future of Automotive Plastic Injection Molding
The future of automotive plastic injection molding looks incredibly promising. As technology continues to evolve, we can anticipate several trends that will shape the industry:
1. Automation and Industry 4.0
The integration of smart technologies and automation in manufacturing processes will enhance efficiency and output. Predictive maintenance and real-time data analysis will optimize production lines.
2. Lightweight Materials
With the continuous push for fuel efficiency, the automotive industry will likely see increased use of innovative and lightweight materials, such as composite plastics.
3. Focus on Circular Economy
Many companies are moving towards a circular economy model, emphasizing recycling and reusing materials. This shift not only aids sustainability but also addresses consumer demand for eco-friendly products.
Conclusion: The Role of Automotive Plastic Injection Molding Companies in Shaping the Industry
In conclusion, automotive plastic injection molding companies are playing a pivotal role in transforming the automotive manufacturing landscape. By leveraging technologies, embracing sustainability, and maintaining a relentless commitment to quality, these companies are contributing to a more efficient, cost-effective, and eco-friendly industry. As they continue to innovate and adapt, the potential for growth remains boundless.
For more information about leading practices and exceptional solutions in the domain of automotive plastic injection molding, visit Deep Mould today.