The Ultimate Guide to Concrete Mixing Plants
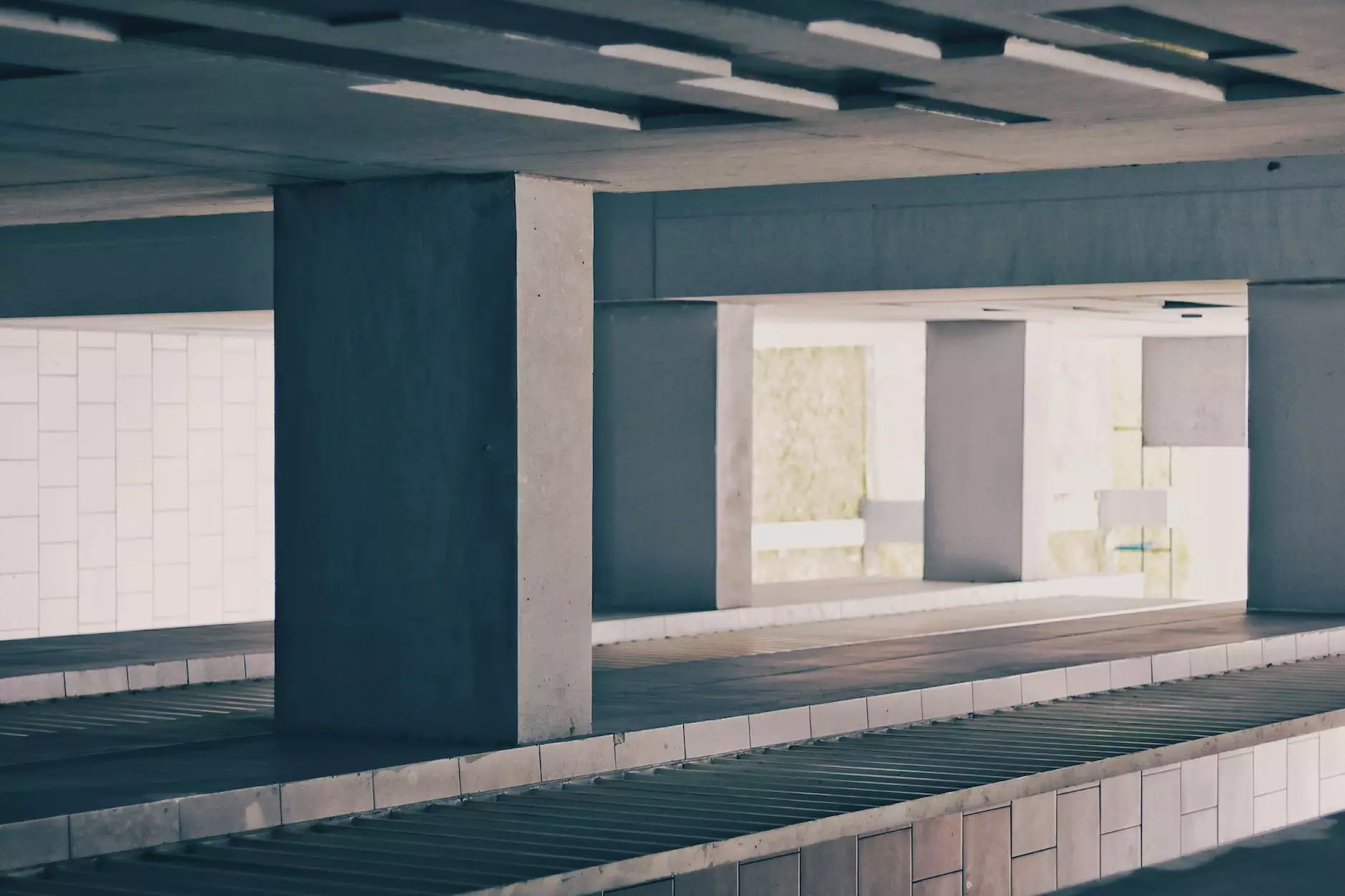
The construction industry is evolving rapidly, driven by technological advancements and an increasing demand for quality materials. One of the most critical components of modern construction is the concrete mixing plant. This article dives deep into the world of concrete mixing plants, examining their significance, the variety of types available, and their impact on the construction process.
What is a Concrete Mixing Plant?
A concrete mixing plant is a facility where various ingredients, including water, aggregate, cement, and additives, are blended together to produce concrete. This concrete is essential for various construction projects, ranging from residential homes to massive infrastructure projects such as bridges and highways.
Components of a Concrete Mixing Plant
Understanding the components of a concrete mixing plant is vital for appreciating its functionality. The main parts include:
- Cement Silo: Stores cement and ensures a continuous supply.
- Aggregate Bins: Hold different types of aggregates like sand, gravel, or crushed stone.
- Concrete Mixer: The heart of the plant where materials are combined.
- Control System: Manages the mixing process and monitors outputs.
- Water Supply System: Ensures consistent water supply for mixing.
Types of Concrete Mixing Plants
There are several types of concrete mixing plants, each tailored to specific needs and project scales. The most common types include:
1. Stationary Concrete Mixing Plants
Stationary plants are typically set up in a single location for long-term projects. They are designed for high production capacities and can operate continuously. These plants are ideal for large construction sites where a consistent supply of concrete is required.
2. Mobile Concrete Mixing Plants
Unlike stationary plants, mobile concrete mixing plants are portable, allowing them to be relocated easily. They are perfect for smaller projects or temporary jobs where site conditions may change frequently. Their compact design facilitates easy transport and setup.
3. Batch Mixing Plants
In batch mixing plants, ingredients are combined in batches. This method allows for precise control over the mix design, making it ideal for specialized concrete types. Batch processing is suited for projects requiring varying concrete strengths and properties.
4. Continuous Mixing Plants
Continuous mixing plants operate non-stop and are designed for high-efficiency production. They are generally utilized in projects with a continuous demand for concrete, such as road construction and large-scale manufacturing.
Benefits of Using a Concrete Mixing Plant
Investing in a concrete mixing plant offers numerous benefits that can significantly enhance a construction project's efficiency and outcome. These include:
- Quality Control: With precise measurements and the ability to tailor concrete mixes, plants ensure consistent quality.
- Cost-Effectiveness: Over time, the use of a concrete mixing plant can lead to significant cost savings by reducing material waste and labor costs.
- Time Efficiency: Continuous and automated mixing processes save time on-site, allowing for faster project completion.
- Customization: Enables the production of a wide variety of concrete mixes, tailored to specific project requirements.
- Reduced Material Waste: Efficient mixing techniques minimize excess material, contributing to a greener construction process.
How to Choose the Right Concrete Mixing Plant
Selecting the right concrete mixing plant involves considering several factors that align with your project needs:
1. Production Capacity
Evaluate the amount of concrete required for your project to determine the appropriate capacity of the plant, whether stationary or mobile.
2. Project Duration
For long-term projects, a stationary plant is advisable. In contrast, mobile plants suit short-term or smaller projects.
3. Type of Concrete Required
Consider the specific types of concrete mixes you need, such as standard, high-strength, or specialized concrete, and choose a plant that accommodates these requirements.
4. Budget Constraints
Your budget will play a crucial role in your selection. Assess the initial investment against long-term savings and operational costs.
Maintenance Best Practices for Concrete Mixing Plants
- Routine Inspections: Conduct daily inspections to identify wear and tear or any malfunctions early.
- Cleaning: Regularly clean the mixer and associated components to prevent contamination and ensure product quality.
- Calibrating Equipment: Ensure all weighing and mixing equipment is calibrated for accurate measurements.
- Lubrication: Regularly lubricate moving parts to reduce friction and wear.
- Monitoring Performance: Utilize the control system to monitor the plant's efficiency and identify any potential issues promptly.
Innovations in Concrete Mixing Technology
The concrete mixing industry is benefiting from several innovative technologies that enhance efficiency and sustainability:
1. Automation and Control Systems
Advanced control systems allow for automated batching and mixing processes, significantly reducing manual labor and the potential for human error.
2. Sustainability Initiatives
Innovations such as recycling concrete and utilizing eco-friendly materials have become prevalent, promoting sustainability in the construction industry.
3. Smart Concrete Technology
Integrating sensors into concrete allows real-time monitoring of strength and durability, ensuring structural integrity and performance.
The Role of Polygon Mach in Concrete Mixing Plant Solutions
At Polygon Mach, we specialize in providing high-quality concrete mixing plants designed to meet the diverse needs of the construction industry. Our cutting-edge solutions prioritize efficiency, cost-effectiveness, and sustainability.
Why Choose Polygon Mach?
- Expertise: Our team consists of industry experts with years of experience in concrete technology.
- Custom Solutions: We offer tailor-made plants to match specific project requirements and conditions.
- Quality Assurance: Each plant is manufactured to the highest standards, ensuring durability and reliability.
- After-Sales Support: We provide comprehensive after-sales services, including maintenance and support, ensuring optimal performance post-purchase.
Conclusion
The concrete mixing plant is a fundamental component of modern construction, playing a crucial role in producing high-quality concrete for various applications. Understanding the types, benefits, and innovations associated with concrete mixing plants is essential for anyone involved in the construction industry. Choosing the right plant, maintaining it properly, and staying updated with the latest technological advancements can significantly enhance project success.
Invest in a reliable concrete mixing plant from Polygon Mach to optimize your construction projects, ensuring quality, efficiency, and sustainability in every mix.