The Ultimate Guide to Turbo Charger Manufacturing
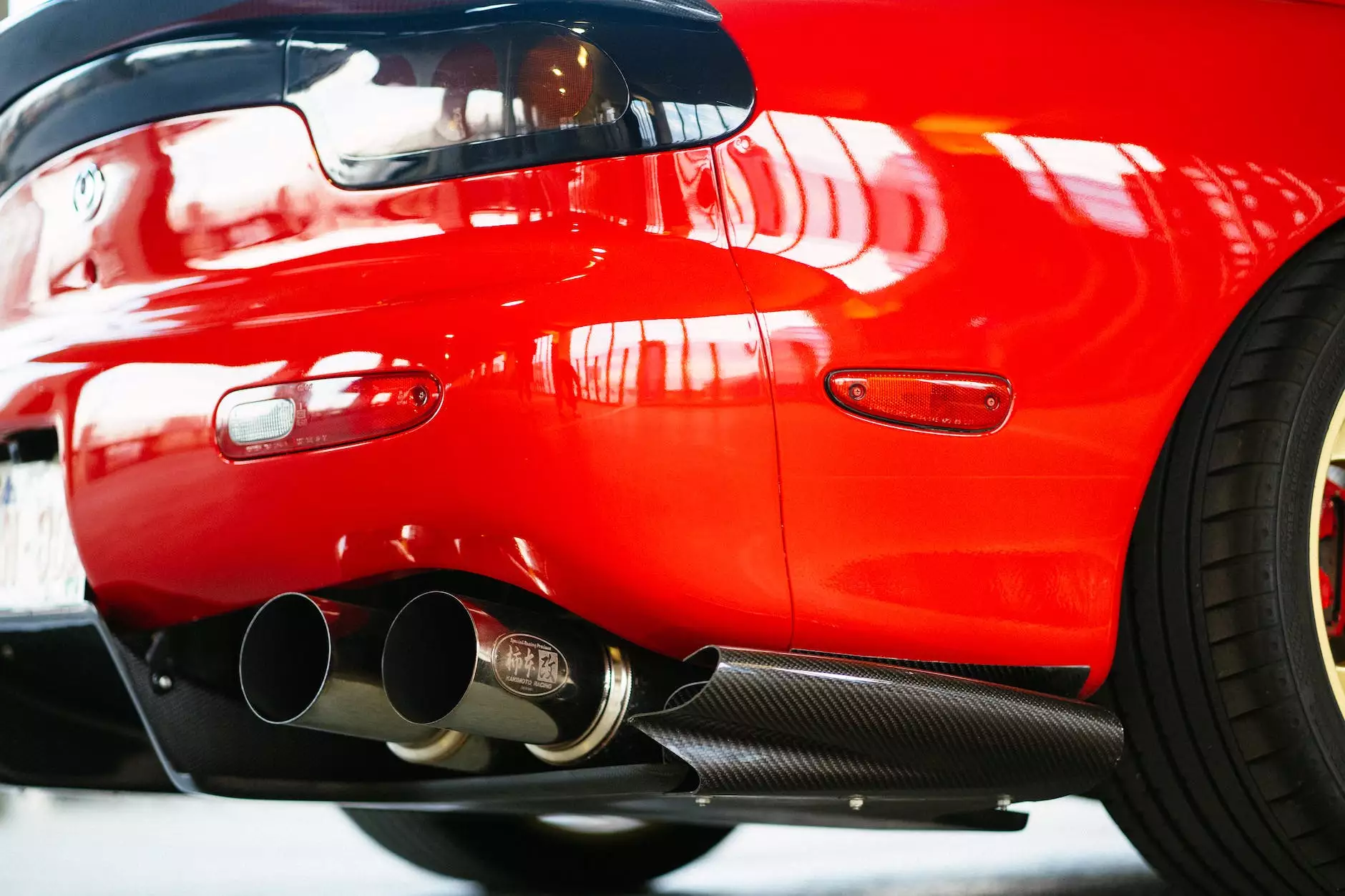
In today's rapidly evolving automotive and industrial sectors, the role of a turbo charger manufacturer has become increasingly significant. Turbochargers are pivotal in maximizing engine performance, enhancing efficiency, and reducing emissions. This comprehensive guide will explore the intricate world of turbo charger manufacturing, from the fundamentals of turbochargers to cutting-edge production techniques, and quality assurance processes essential for excellence in the industry.
Understanding Turbochargers: What They Are and How They Work
A turbocharger is an essential component in many modern diesel engines. By recycling exhaust gases to boost engine air intake, turbochargers significantly enhance efficiency and power output. Here’s a simplified breakdown:
- Efficiency: Boosts power without increasing the engine size.
- Performance: Improves throttle response and acceleration.
- Environmental Impact: Reduces emissions by ensuring more complete combustion.
Key Components of Turbo Chargers
To understand the manufacturing process, one must first grasp the fundamental components of turbochargers:
1. Turbine
The turbine transforms exhaust energy into mechanical energy. Ensuing this, it drives the compressor, which forces more air into the engine.
2. Compressor
This component pushes the compressed air into the engine’s combustion chamber, allowing for a higher fuel-air mixture, enhancing power.
3. Bearing System
Critical for minimizing friction between the moving parts, the bearing system ensures smooth operation.
4. Housing
Typically made of heat-resistant materials, the housing protects the internal components from extreme temperatures and pressures.
The Manufacturing Process of Turbo Chargers
The process of manufacturing turbochargers involves several intricate steps, each critical to ensuring the final product's quality and performance.
1. Material Selection
High-quality materials are essential for durability and performance. Common materials include:
- Cast Iron: Used for turbine housing due to its heat resistance.
- Aluminum Alloys: Preferred for the compressor wheel for its lighter weight.
- Stainless Steel: Utilized for components needing superior resistance to oxidation.
2. Precision Machining
Components are meticulously machined to ensure precise tolerances. This is crucial for the performance of the turbocharger, as even minute discrepancies can lead to severe consequences.
3. Balancing
Each component must be balanced to prevent vibrations that can cause premature failure. Dynamic balancing machines are employed to achieve this.
4. Assembly
The assembly process involves combining the components with utmost care. This process often utilizes advanced technologies, including robotics, to ensure accuracy and efficiency.
Quality Control in Turbo Charger Manufacturing
Ensuring the reliability and performance of turbochargers requires rigorous quality control protocols. Here are key quality assurance steps:
1. Inspection of Raw Materials
Before production begins, materials undergo thorough inspection to ensure they meet strict industry standards.
2. In-Process Testing
During manufacturing, components are frequently tested for dimensional accuracy, material integrity, and performance metrics.
3. Final Testing
Completed turbochargers face extensive testing in simulated operating conditions to verify their performance and reliability.
Trends Influencing the Turbo Charger Manufacturing Industry
The landscape of turbo charger manufacturing is continually evolving, influenced by technological advancements and market demands. Here are some notable trends:
1. Increasing Demand for Fuel Efficiency
As environmental concerns grow, the demand for more fuel-efficient vehicles drives the need for advanced turbocharging systems.
2. Growth of Electric and Hybrid Vehicles
With the rise of electric vehicles, hybrid systems combining turbo chargers with electric motors are being developed.
3. Advanced Materials and Technologies
Ongoing research into lightweight, high-strength materials is pushing the boundaries of turbocharger design and durability.
The Importance of Choosing the Right Turbo Charger Manufacturer
Selecting the right turbo charger manufacturer is crucial for your business. Key considerations include:
1. Reputation and Experience
A manufacturer with a proven track record will likely deliver high-quality products and reliable service.
2. Innovation and Technology
Companies that invest in research and development often lead the market in product performance and efficiency.
3. Customer Service
Responsive and knowledgeable customer service can make a significant difference in your operational success.
Conclusion: The Future of Turbo Charger Manufacturing
In conclusion, the role of a turbo charger manufacturer is pivotal in shaping the future of automotive engineering and environmental sustainability. As industry demands shift and technology evolves, it is essential to remain informed about the latest manufacturing techniques, materials, and innovations that will drive success in this competitive industry. At Client Diesel, we pride ourselves on being at the forefront of turbo charger manufacturing, delivering top-quality products while ensuring optimum performance and reliability for our customers.
By investing time in understanding the intricacies of turbocharger manufacturing, businesses can significantly enhance their operational efficiencies, lower their environmental footprints, and ultimately, boost their bottom line.